Situation
One of the largest medical technology companies, with over 100 global plants, faced significant raw material delays from a key supplier, impacting two US sister plants producing similar products.
Without a structured system for raw material distribution, production schedules were disrupted. Manual production planning further worsened the issue, leading to a $5 million backorder pileup, impacting business performance and customer commitments.
Objectives
To overcome supply chain inefficiencies and reduce the significant backorder pileup, the company wanted to automate and optimize raw material allocation and production planning.
They needed a data-driven tool that could:
- Generate a day-level ‘should-build’ plan on a weekly basis, aligning production with demand, capacity, and raw material availability.
- Automate purchase order generation based on demand segments and production line capacity.
- Optimize raw material distribution between plants to maximize production efficiency and minimize delays.
Mu Sigma’s Approach
We stepped right in and implemented a data-driven, algorithmic approach to optimize production planning and raw material allocation. By leveraging advanced analytics, the team enabled smarter decision-making and streamlined operations across plants. Here’s what we did:
- Demand Segmentation: Classified demand into four segments—critical backorders, tender orders, regular backorders, and base demand—to prioritize production.
- Allocation Logic Development: Created a custom logic to distribute raw materials based on production time, capacity, inventory, and demand segment
- Algorithm Design: Developed an advanced algorithm that incorporated variables such as demand, inventory levels, production capacity, and scrap rate to create an optimal production plan.
- Built a Supplier Scheduling Tool: Deployed an automated tool that
- Identifies raw material shortages to generate precise purchase orders.
- Provides detailed lists of raw materials for allocation, shipping, and production.
- Automates day-level ‘should-build’ plans displayed at the sub-assembly level.
- Presents graphical views of pre-production, in-production, and post-production metrics.
Impact
The Supplier Scheduling Tool significantly improved raw material management, optimized allocation between plants, and enhanced operational efficiency with automated planning and real-time insights. With these improvements, the client achieved:
- 50% reduction in backorders within three months (over $2.5M reduction)
- Elimination of $2 million worth of production delays
Business Impact
-
50%
reduction in backorders within 3 months
-
$2 Mn
worth of production delays eliminated
Let’s move from data to decisions together. Talk to us.
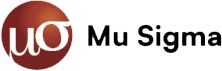
The firm's name is derived from the statistical terms "Mu" and "Sigma," which symbolize a
probability distribution's mean and standard deviation, respectively.