Situation
A consumer electronics company struggled with in-warranty repair forecasts, leading to over-predictions that drained cash flow and operational efficiency. They needed a data-driven overhaul to optimize reverse logistics.
Challenge
The company faced pressing issues:
- Inaccurate forecasts, relying on heuristic approaches and extensive manual intervention.
- Frequent fluctuations in repair predictions, impacting inventory, cash flow, and resource allocation.
- Lack of automation, leaving the system vulnerable to errors and inefficiencies.
Approach
Mu Sigma engineered a comprehensive transformation leveraging advanced analytics and proprietary tools:
- Developed a unified forecasting framework tailored for workforce management, inventory optimization, and quality control.
- Deployed muFlow, our orchestration and automation workbench, to centralize and streamline model management.
- Built an automated anomaly detection system using six algorithms to identify fraud and manufacturing defects early.
- Created a single source of truth framework, consolidating forecasts across multiple business functions for consistency and precision.
- Our integrated approach ensured scalability, responsiveness, and data-driven efficiency in managing reverse logistics.
- Integrated the solution with existing search engines, eliminating translation delays and enabling seamless cross-language searches.
The advanced system enabled adaptive and intelligent search strategies, reducing manual effort and ensuring relevance in results.
Impact
- Over $330 million in cost savings, achieved through streamlined operations and optimized logistics.
- 98% improvement in forecast accuracy, eliminating over-predictions and stabilizing cash flow.
Business Impact
-
$330M+
in cost savings
-
98%
improvement in forecast accuracy
Let’s move from data to decisions together. Talk to us.
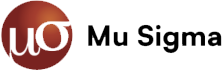
The firm's name is derived from the statistical terms "Mu" and "Sigma," which symbolize a
probability distribution's mean and standard deviation, respectively.